
I once worried about confusing manufacturing steps, wasted time, and unpredictable costs. I decided to simplify the process. Now I focus on helping you avoid pitfalls. I want you to feel confident about how enamel pins are crafted.
Enamel pins are created by turning a digital design into a metal mold, stamping the design into a base, adding plating, and finally filling it with enamel color. Each step ensures smooth surfaces, bright colors, and accurate details for collectors and businesses.
I remember a large buyer from France who almost gave up because of production delays. I shared the step-by-step approach. He stayed intrigued and discovered how these pins get their vibrant details.
Formenbau
I begin by converting a digital file into a physical mold. This transforms my design ideas into reality. This mold becomes the foundation for the rest of the production steps.
I upload my finalized design into a specialized machine that carves it out in steel. Then I remove extra metal to shape the mold. Repeated heating and cooling hardens the mold so it can withstand high-pressure stamping. This step creates a precise, durable base.

Dive Deeper into Mold Creation
I learned the importance of strong molds after a previous batch shattered under stress. That mishap forced me to test new steel alloys. Now I rely on high-grade industrial steel. Heat treating it ensures the mold won’t crack when used on softer metals like iron or zinc alloy. Below is a brief overview:
Step | Action | Why It Matters |
---|---|---|
Digital File | Finalize pin artwork in vector form | Ensures crisp outlines |
CNC Cutting | Machine carves out design in steel | Achieves exact details |
Heat Treat | Repeated heating and cooling cycles | Increases mold strength |
Excess Trim | Cut off surplus metal material | Helps mold fit machinery |
I value precision because a flawed mold can ruin hundreds of pins. Maintaining strict quality checks helps me avoid wasted materials and time.
Stamp the Pattern and Cut out the Pins
After the mold is ready, I stamp the pin shape into softer metal. This is where the design takes a physical form.
I place the hardened steel mold into a stamping machine. Then I press it with about five tons of force onto an iron or zinc alloy plate. Next, a separate machine punches out the final shape of the pin. This is also when I solder on the pin backing.
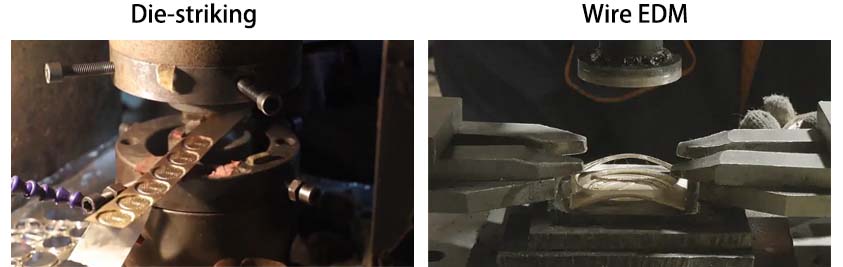
Dive Deeper into Stamping
I remember my first stamping session with Mark Chen, a confident French buyer who wanted to see how we transform designs into 3D shapes. He was fascinated by the thunderous press noise. This step requires consistent pressure. If the machine is off by even a fraction, the design gets misaligned.
Key Considerations:
- Metal Choice: Iron or zinc alloy is common. They are affordable and soft enough for high-detail stamps.
- Machine Calibration: I test pressure levels before each run. Precise calibration prevents double impressions and preserves the mold.
- Soldering the Backing: I attach the clasp while the pin is still warm. This approach ensures a solid joint, reducing risk of breakage.
I sometimes face time constraints if I have large orders from the United States or Europe. Keeping four production lines running helps me stay on schedule, but I still prioritize correct machine setup over speed. I want to avoid final pins with mismatched outlines.
Electroplated
Next, I prepare soft enamel pins for electroplating. This step gives the pins their metallic finish or dyed color. It’s also where the pins begin to look polished.
Soft enamel pins get electroplated first. An electric current passes through a special solution, bonding the chosen metallic finish (like gold or silver) onto the pin. Soft enamel pins can also be color-dyed in any Pantone shade if you prefer non-metallic outlines.
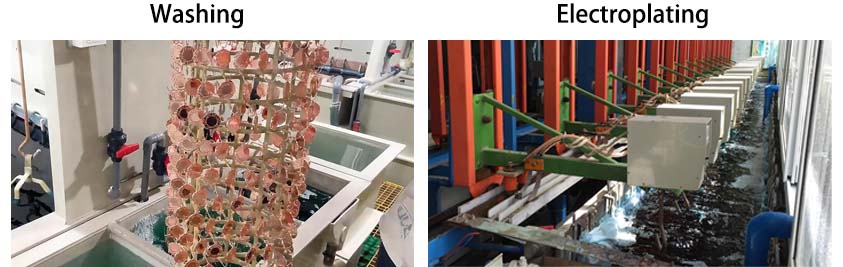
Dive Deeper into Electroplating for Soft Enamel
I was initially baffled by the electroplating science. Now I see it like a magic bath. The positive ions from the plating metal deposit onto the negative pin base. This plating ensures consistent color and adds a protective layer.
Common Finishes:
- Gold: Popular for luxury appeal.
- Silber: Classic, reflective look.
- Antikes Messing: Retro effect, suits vintage themes.
- Color Dye: If I need pink outlines or other unusual colors, I rely on dye instead of metallic plating.
I notice that sporting goods companies often prefer traditional gold or silver for awards. Meanwhile, travel companies or museums might ask for more experimental colors. Electroplating is a key stage. If I don’t maintain a clean solution or stable current, the final surface could appear dull or uneven.
Enamel and Bake
This is when the pins get their splash of color. Whether it’s soft enamel or hard enamel, the process involves carefully applying enamel paint and baking it.
During soft enamel, I fill recessed areas with thin paint, leaving the pin’s edges raised. For hard enamel, I fill color all the way to the brim, then bake it. I either use a machine injector or do it by hand. Afterwards, the paint hardens in an oven.
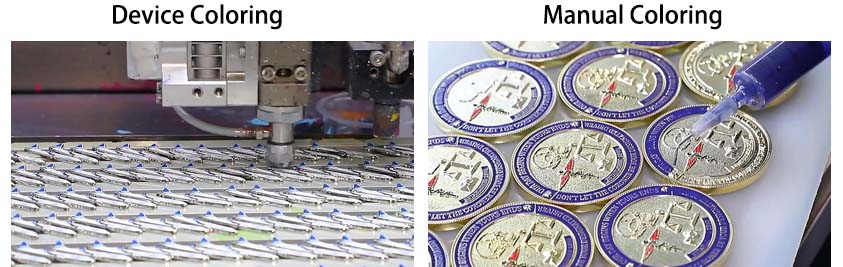
Dive Deeper into Enamel Application
I find enameling to be the most visually satisfying step. I’ve seen delicate ramen soup designs or intricate three-eyed foxes come alive when color is added. I use either automated tools or manual techniques:
Enamel Application Methods (Soft vs. Hard)
Typ | Application Style | Final Look | Typical Use Cases |
---|---|---|---|
Soft Enamel | Thin layer, recessed below edge | Textured, visible metal borders | Complex line art, cost-effective |
Hard Enamel | Filled to level of metal edges | Flat, glossy, more durable | Premium pins, polished final finish |
At this point, I notice customers like Mark Chen often choose soft enamel for tourist commemorative coins because it’s cheaper and features more color outline options. Corporate buyers looking for a heavyweight look sometimes pick hard enamel. Keeping track of client needs is essential. If I fill the enamel incorrectly, the final product looks sloppy, and I risk rework.
Polish
After soft enamel pins are baked, they’re nearly complete. However, hard enamel pins require extra polishing to ensure a perfectly even surface.
Hard enamel pins get polished to remove any unevenness between metal edges and paint. This extra step makes them smooth and reflective. Polishing is critical for achieving that glossy, high-end feel. Customers often mention how polished hard enamel pins appear more premium.
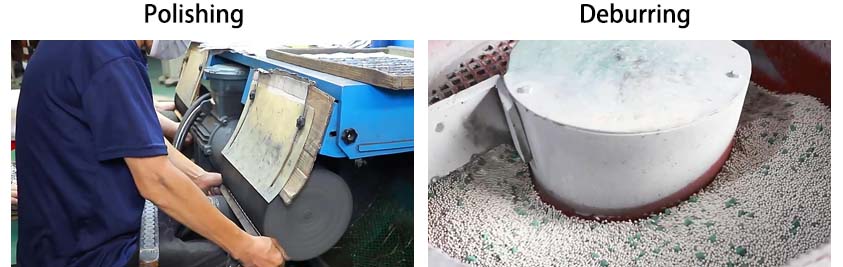
Dive Deeper into Polishing Hard Enamel
I view polishing as a final finishing chore for top-tier enamel pins. The process involves specialized buffing wheels and compounds. If I skip or rush polishing, the metal lines might feel rough. That tarnishes the entire design.
Polishing Tips:
- Correct Grit Compound: I start with a coarser compound, then move to a fine one.
- Sicherheitsausrüstung: The buffing wheel can spin fast, so I wear protective gloves.
- Time Investment: Polishing each pin thoroughly is time-consuming, but it’s essential to impress discerning collectors.
Brands in Russia, France, or the UK often request hard enamel for high-profile events or product launches. The polishing step raises production costs slightly, but it also boosts perceived value. I prefer perfect finishes over cutting corners.
Electroplated
Now it’s time for the hard enamel pins to get plated. Because the enamel is fully set, the plating only bonds to exposed metal edges.
Hard enamel pins head back to the electroplating bath. This second plating step applies the same principle of using electrical current to deposit metal molecules onto the pin’s metal edges. It keeps the enamel colors crisp, as those sections do not conduct electricity.
Dive Deeper into Electroplating for Hard Enamel
I think of it like a second chance to add a refined metallic sheen. I keep a close watch on the plating bath temperature and pH levels. A mismatch could lead to spots or color defects.
Common Issues and Solutions:
- Uneven Coating: Adjust the clamp or wire arrangement so each pin is fully exposed.
- Discoloration: Replace contaminated electrolyte solution or fix voltage levels.
- Time in Bath: Overplating might cause lumps or a dull finish, so I carefully time each batch.
I had an order for a major museum in the United States. They requested gold outlines on a hard enamel collection featuring historical figures. That second plating pass made the edges pop brilliantly. Checking each detail gave me peace of mind.
Screen Printing Details
Sometimes I need extra details that enamel alone can’t achieve. Screen printing allows me to add text or tiny logos on top of the design.
This step is optional. If the design calls for extremely fine details or multiple logo colors, I use screen printing. I layer ink on top of the baked enamel. Then I let it cure, resulting in crisp lines and vibrant text that enamel can’t replicate.
Dive Deeper into Screen Print on Enamel
I originally avoided screen printing due to cost, but certain clients insisted on tiny, intricate designs. The Ray Ban logo on sunglasses is a classic example. I produce complex brand elements more accurately through printed ink.
Process Breakdown:
- Prepare the Screen: I coat a fine mesh with a light-sensitive emulsion.
- Expose and Rinse: A template blocks areas where ink shouldn’t pass.
- Apply Ink: I use a squeegee to press ink through the mesh onto the pin.
- Curing: The printed layer must dry thoroughly to avoid smudges.
I love seeing how this step can elevate a design. A museum might request a small tagline on a special edition coin. Without screen printing, these words might be too small to enamel accurately.
Quality Control
Finally, no product leaves my factory without a final inspection. I call this the “last line of defense.”
Quality assurance involves checking for scratches, color flaws, or faulty backings. I do this by hand, verifying that each pin meets my standards for color accuracy, plating smoothness, and clasp strength. Only then do I package the pins for delivery.
Dive Deeper into Quality Assurance
I rely on a consistent checklist. One of my biggest frustrations is shipping an order overseas, only to learn half the pins had minor defects. That hurts my brand reputation. So I prefer to screen them thoroughly.
My QA Checklist:
Checkpoint | What I Look For |
---|---|
Color Accuracy | Compare enamel color to Pantone swatch |
Metal Finish | Confirm plating has no patches |
Attachment Strength | Ensure soldered clasp doesn’t wiggle |
Surface Imperfections | Look for scratches or bubbles |
Since I do B2B wholesale only, large corporate buyers expect uniform quality across bulk orders. I notice my sporting goods clients appreciate consistent color. Travel companies often focus on strong clasps that won’t pop off easily. Delivering reliable pins keeps me competitive on Alibaba, exhibitions, and my own website.
Packaging and Shipping Preparation
After passing final QA, I prepare them for packaging, labeling, and shipping. Proper packaging protects pins from damage in transit.
I often pack bulk orders in sturdy boxes with foam padding or individual poly bags. This step helps me reduce the risk of scratches during shipping. I label everything clearly to streamline customs checks and ensure timely delivery.
Labeling and Documentation
I print labels with product details, quantity, and shipping addresses. My export documents must satisfy import regulations for the United States, Russia, France, and beyond. Mark Chen once shared how delayed paperwork cost him a sales season. I prioritize accuracy to prevent that.
Freight Options
- Air Freight: Quicker but costs more.
- Sea Freight: Economical but takes longer.
- Express Services: Great for urgent samples or small-batch orders.
A French museum client once ordered special edition challenge coins. They paid extra for air freight to meet their exhibit launch. I juggled the final QA, packaging, and express shipping to meet their deadline.
Communication Tips
I share shipping updates in real time. Miscommunication can lead to lost parcels. Some buyers come from countries with strict customs. I have experience handling these procedures. Regular email updates keep everyone informed.
Abschluss
I transform simple digital designs into beautiful enamel pins through precise molding, stamping, plating, enameling, and final QA. My focus is consistent quality, and I stay mindful of each step so every pin meets high standards.