The challenge coin creation process involves several steps, from crafting a custom mold to final quality inspection. Here’s an overview:
- Creating the Custom Mold: Transfer the customer’s design into a metal mold that will imprint the coin.
- Stamping the Coin: Press the mold onto a metal blank to form raised designs and text.
- Trimming Edges: Cut the coin edges precisely to achieve a smooth, custom shape.
- Polishing and Deburring: Remove burrs and refine the surface to enhance smoothness and shine.
- Electroplating: Add a protective metal layer, available in finishes like gold, silver, antique bronze, or black nickel.
- Color Filling: Apply enamel colors matched to Pantone codes, then bake for durability.
- Laser Engraving: Engrave personalized details, such as text or serial numbers, on the coin’s surface or edge.
- Quality Control: Inspect each coin for appearance, color uniformity, and finishing quality before packaging.
This step-by-step process ensures each custom challenge coin meets high standards for detail, durability, and design.
Creating the Custom Coin Mold
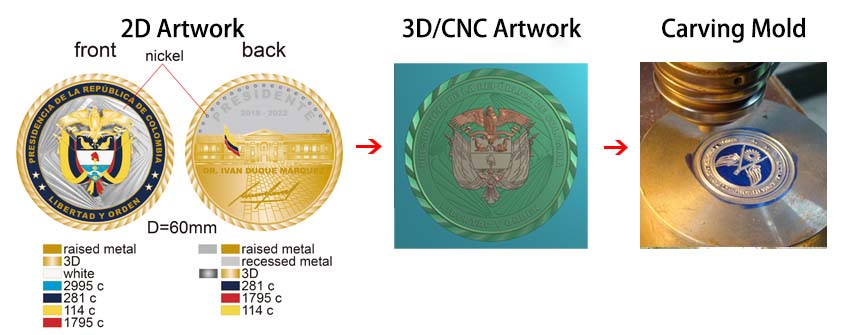
The first step in crafting a challenge coin is designing and creating a custom mold. This process involves transferring the customer’s artwork into a metal mold, which will be used in later steps to stamp the design onto metal.
First, our design team creates a 2D drawing and confirms it with the customer. Once the 2D drawing is approved, the team converts the patterns, text, and logos into 3D design files that capture the depth and raised areas of the artwork, ensuring the final coin will have the desired look and feel. After verifying that the 3D design files match the 2D drawing, these 3D design files are transferred to the CNC engraving machine. The CNC machine then precisely carves every detail onto the metal mold.
To ensure precision, we create separate molds for the front and back of the coin. Once the CNC machine finishes engraving, we test the molds by striking soft metal blanks and examining the impressions they leave. If any imperfections are found, we can make adjustments at this stage.
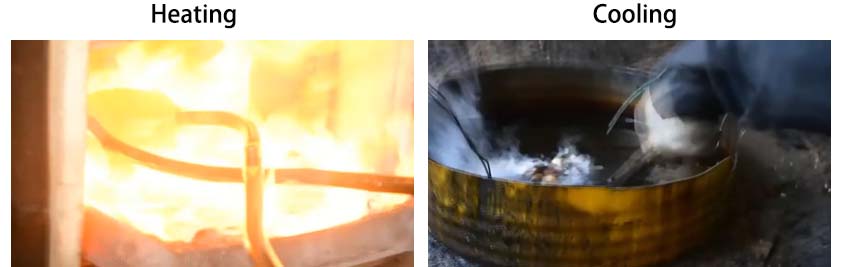
Once we’re satisfied with the molds, we heat-treat them in a high-temperature oven, hardening the steel so it can withstand the intense pressure of stamping. When the molds are red-hot, we remove them from the oven and douse them in cool oil. It takes anywhere from 500 to 1,000 tons of force to stamp a brass coin, and heat-treating the molds beforehand ensures they are ready to handle the task.
The quality of the mold is critical, as it directly affects the clarity and accuracy of every detail on the coin. This precise mold-making process ensures each design element is clearly replicated on the final coin.
Stamping the Coin
The stamping process, also known as die striking, uses custom-made coin molds (sometimes called dies) to press the design into the metal. While this sounds straightforward, the approach can vary based on the shape and type of coin being created.

For round coins, we typically start with coin blanks. These blanks are plain, circular metal discs cut from strips of brass or steel. To create them, we feed brass or steel strips through a coin press equipped with a circular cutting tool. The press punches out the round blanks, which are then set aside for the die striking process. When ready, the coin blanks are placed between the molds on a high-pressure coin press, which strikes the molds into the blanks to imprint the raised design. Finished challenge coins are usually between 1.5” and 2” in diameter, so we adhere to these standard sizes when creating blanks.
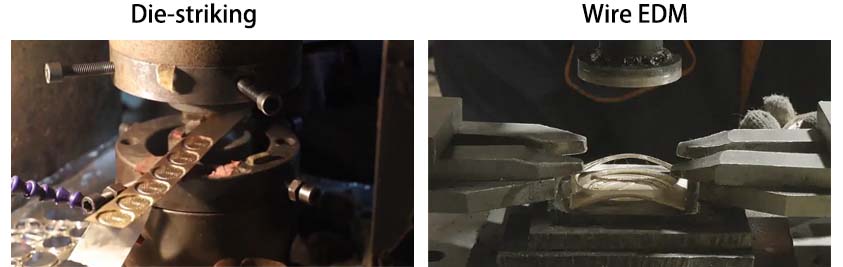
For custom-shaped coins, the die striking process is slightly different. Instead of cutting blanks first, we feed a continuous brass strip through the press and stamp multiple impressions of the design along its length. After stamping, we use a custom-shaped cutting tool to trim out each coin along its unique outline. These custom-shaped cutting tools are made with Wire EDM technology, which allows us to produce tools for anything from simple circles to the most intricate shapes.
Just like the coin molds, the cutting molds undergo trimming and heat treatment to ensure durability and precision. Once the cutting mold is prepared, it is loaded onto a special coin press. When this press comes down on the brass strip, it precisely cuts out each coin with the design impression already in place.
Trimming the Coin Edges
After stamping, the coin’s edges need precise trimming to achieve either a standard round shape or a custom shape specified by the customer.
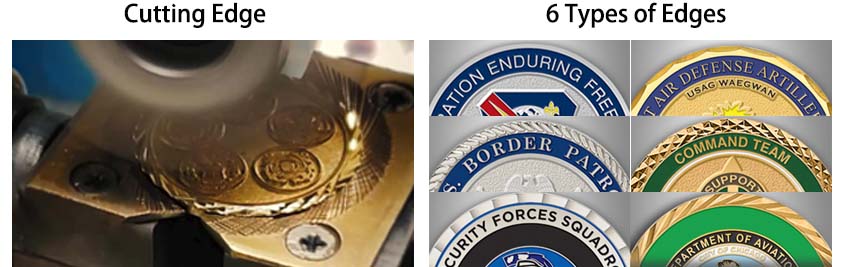
This step typically uses specialized cutting molds or punches to create smooth, even edges. Edge trimming not only impacts the coin’s appearance but also its feel, so precision is essential here.
Customers can also choose to add unique edge effects, like reeded or diamond-cut edges. These effects add texture and visual appeal, enhancing the overall quality of the coin.
Polishing and Deburring
After trimming, the coins may have tiny burrs or uneven textures on their edges or surfaces, which are removed by polishing.
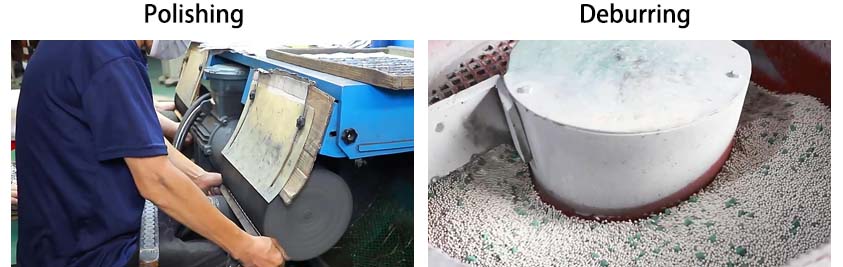
Polishing removes any burrs, making the edges and surfaces smoother and more refined while also enhancing the coin’s shine, adding to its overall aesthetic appeal. This step is typically done in a specialized polishing machine, using specific materials and tools to achieve the ideal level of smoothness and brightness.
Various polishing methods offer different finishes, from a high-gloss mirror effect to a soft matte look, and can be customized based on customer preference.
Electroplating
After polishing, the challenge coins go through an electroplating process that adds a protective layer to the surface, enhancing the coin’s appearance and durability. Electroplating is a precise chemical process with multiple steps to ensure a uniform, long-lasting finish.
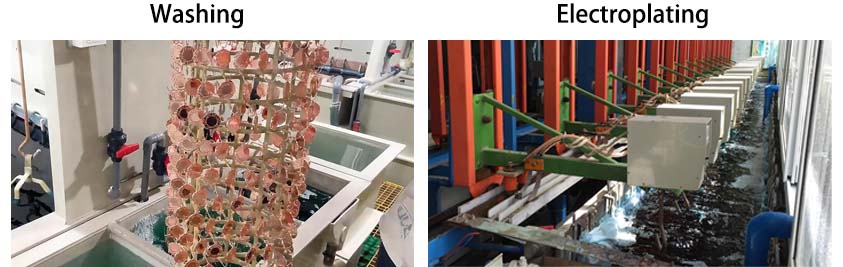
First, the coins are hung on copper wires and immersed in clean water, followed by different chemical solutions to fully clean the surfaces. This ensures the coins are free of any impurities, allowing for an even coating. Once cleaned, the coins are submerged in a solution containing precious metals, such as gold, silver, or copper, to begin the actual plating process.
During electroplating, an electric current runs through the solution, bonding metal ions securely to the coin’s surface. Popular electroplating colors include gold, silver, antique bronze, black nickel, and rainbow finishes. This process creates a thin but durable custom layer of metal on each coin. Electroplating enhances the coin’s visual appeal and provides corrosion and wear resistance, extending the coin’s lifespan.
Depending on customer requirements, coins can be given a single-color plating, multi-layer plating, or an anti-oxidation coating to maintain their brilliant appearance over time.
Color Filling
For challenge coins with colored designs, the next step is color filling. This process typically uses enamel paint to fill the recessed areas of the design, ensuring colors are vivid and durable. Color filling can be done manually or by machine, but for smaller orders of around 200 coins, hand-filling is usually faster and more efficient.
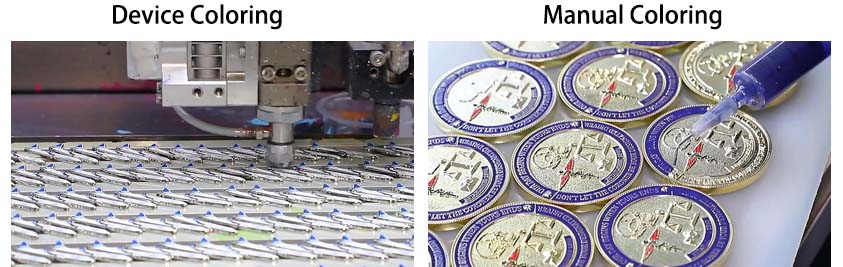
Professional factories use special tools filled with soft enamel paint to precisely fill the recessed areas in each design. Before filling, each color is carefully selected according to the Pantone color code to ensure the final design accurately matches the original. Once all colors are added, the coins are placed in an oven to cure. This baking process hardens the enamel, ensuring it bonds securely to the coin’s surface and enhancing durability.
Differences Between Soft Enamel and Hard Enamel:

For soft enamel coins, colors are filled within the recessed areas of the design, separated by raised metal lines, giving the coin a textured and layered look. The soft enamel paint sits below the metal surface, creating a dimensional feel. Soft enamel coins are electroplated first and then color-filled, which means the enamel sits on top of the plated metal, making colors appear more vibrant.
In contrast, hard enamel coins follow a different sequence. Hard enamel colors are filled and cured before electroplating. After all colors are filled, the coin undergoes multiple polishing stages to level the enamel with the metal surface, creating a smooth, flush finish. Once the hard enamel is polished, the coin is electroplated, giving the metal and enamel a refined, glossy finish that feels high-end and luxurious.
Whether soft or hard enamel, color filling adds depth to multi-colored challenge coins, enhancing their visual appeal and making them truly stand out.
Laser Engraving
After electroplating and color filling are complete, laser engraving can be used to add personalized elements to the coin. Laser engraving allows for the addition of fine text, serial numbers, or other personalized information on the coin’s surface or edge. The high precision of laser engraving ensures that each letter and symbol is sharply detailed without compromising the overall design of the coin.
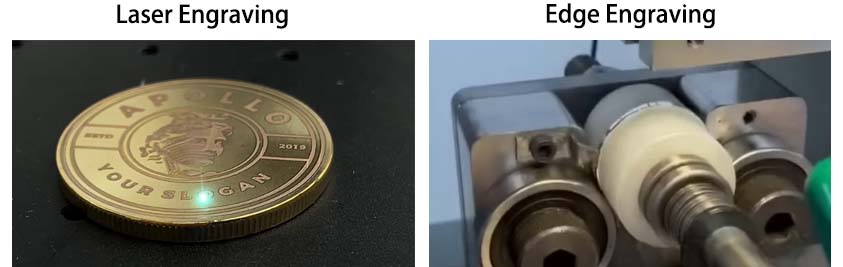
Laser engraving also enables the addition of small details that cannot be achieved through die-striking methods, enhancing the intricacy of the coin’s design. This step not only increases the coin’s uniqueness but also adds commemorative value, making each challenge coin a true reflection of the customer’s personalized requirements.
Quality Control
Once all steps are completed, each challenge coin goes through strict quality control to ensure it meets high standards.

Quality checks include verifying the coin’s appearance, color uniformity, edge smoothness, and polishing quality, making sure every detail matches the customer’s design and expectations. Only coins that pass quality inspection are packaged and shipped.
Our rigorous quality control process guarantees that customers receive flawless coins that meet their expectations and maintain a consistent, high-quality finish.
Get Your Free Challenge Coin Design Now